5S sản xuất là gì? Lợi ích và cách triển khai
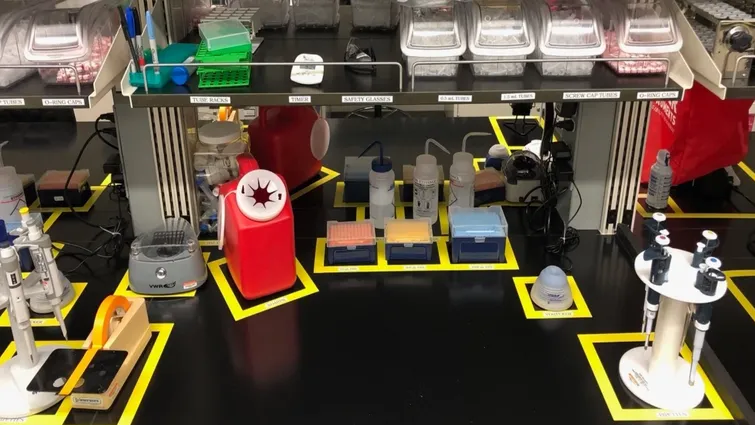
5S sản xuất là phương pháp tổ chức môi trường làm việc theo hướng trực quan, tinh gọn và hiệu quả. Phương pháp này giúp loại bỏ lãng phí, tối ưu năng suất và cải thiện sự an toàn. Khi triển khai 5S sản xuất đúng cách, doanh nghiệp sẽ xây dựng được hệ thống sản xuất chuyên nghiệp và bền vững.
Cấu trúc của phương pháp 5S
5S sản xuất bắt nguồn từ Nhật Bản, gồm năm bước:
- Sort (sàng lọc)
- Straighten (sắp xếp)
- Shine (sạch sẽ)
- Standardize (tiêu chuẩn hóa)
- Sustain (duy trì)
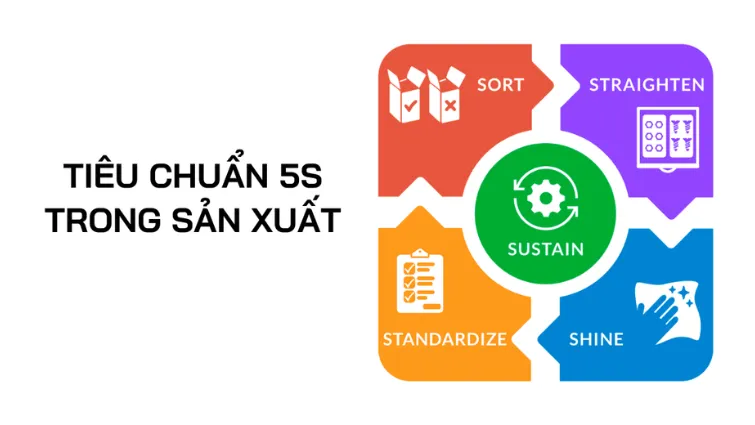
Hình 1. Phương pháp 5S trong sản xuất
Mỗi bước đều đóng vai trò cụ thể trong việc loại bỏ lãng phí và duy trì môi trường làm việc ngăn nắp. Việc thực hiện đúng các bước này giúp phát hiện sớm sự cố như rò rỉ, từ đó nâng cao hiệu quả và độ an toàn vận hành. 5S cũng được mở rộng thành 6S hoặc 5S Plus với yếu tố Safety nhằm tích hợp an toàn vào quy trình.
Tác động đến hiệu quả sản xuất
Một trong những lợi ích lớn nhất của 5S sản xuất là giảm thiểu lãng phí. Theo Taiichi Ohno – cha đẻ Hệ thống sản xuất Toyota, tới 95% chi phí trong sản xuất không tinh gọn là lãng phí. 5S giúp khắc phục khoảng trống thông tin gây ra bởi sự thiếu hướng dẫn rõ ràng trong quy trình công việc. Môi trường trực quan như bảng trực quan hoặc bài học ngắn cho phép nhân viên dễ dàng nhận diện công cụ và quy trình, từ đó giảm thời gian tìm kiếm và sai sót. Đây là một nguyên tắc nền tảng trong phương pháp 5S trong sản xuất.
Tăng năng lực và an toàn cho nhân viên
Theo nghiên cứu của Dugan Laird, người lao động học được 75% kiến thức qua hình ảnh. Việc sử dụng nhãn, biển cảnh báo và hướng dẫn trực quan tại điểm sử dụng giúp truyền đạt quy trình và thông tin an toàn nhanh chóng. Điều này không chỉ hỗ trợ đào tạo mà còn giảm thiểu tai nạn và nâng cao ý thức tự chủ. Một ví dụ tiêu biểu là các nhãn điện ngắt giúp xác định nhanh vị trí ngắt nguồn, hỗ trợ xử lý khẩn cấp. 5S sản xuất kết hợp với các yếu tố của quản lý tinh gọn đã chứng minh hiệu quả thực tế tại nhiều nhà máy công nghiệp lớn.
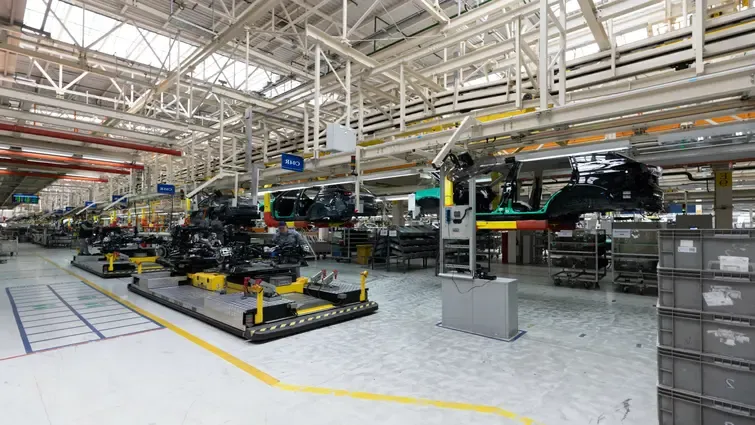
Hình 2. Triển khai 5S trong nhà máy
Hiệu quả kinh tế và minh chứng thực tế
Một nhà sản xuất thiết bị quốc phòng áp dụng 5S sản xuất đã phát hiện nguyên nhân thất thoát công cụ là do không có nhãn và sắp xếp phù hợp. Mỗi ca, nhân viên mất 45 phút tìm kiếm, gây lãng phí lớn. Sau khi triển khai bảng trực quan và phân bổ công cụ theo từng trạm, họ tiết kiệm 1 triệu USD mỗi ngày và giảm 60.000 USD chi phí dụng cụ hàng tháng. Điều này cho thấy tác động rõ ràng khi doanh nghiệp triển khai phương pháp 5S trong sản xuất một cách có hệ thống và toàn diện.
Hướng dẫn triển khai 5S tại nhà máy
Triển khai chương trình 5S nên bắt đầu từ sự kiện cải tiến tại từng khu vực. Doanh nghiệp cần chuẩn bị thẻ đỏ để đánh dấu vật tư không dùng, băng dán sàn, máy in nhãn, biển cảnh báo, thiết bị bảo hộ và khóa an toàn. Tất cả công cụ này góp phần hỗ trợ quy trình sàng lọc, sắp xếp và duy trì không gian làm việc theo chuẩn 5S sản xuất. Ngoài ra, tiêu chuẩn hóa bằng bảng công việc và lịch kiểm tra sẽ giúp duy trì kết quả lâu dài. An toàn phải là yếu tố xuyên suốt và không tách rời từng bước trong triển khai.
Triển khai 5S sản xuất đúng cách giúp nâng cao hiệu quả, giảm thiểu sai sót và cải thiện môi trường làm việc. Doanh nghiệp cần đầu tư đúng bước, đúng công cụ để đạt được lợi ích bền vững. 5S sản xuất không chỉ là công cụ cải tiến mà còn là nền tảng cho hệ thống sản xuất an toàn, hiện đại. Áp dụng nhất quán phương pháp 5S trong sản xuất sẽ tạo ra môi trường làm việc chuyên nghiệp và đầy tính cạnh tranh.